Lean Management
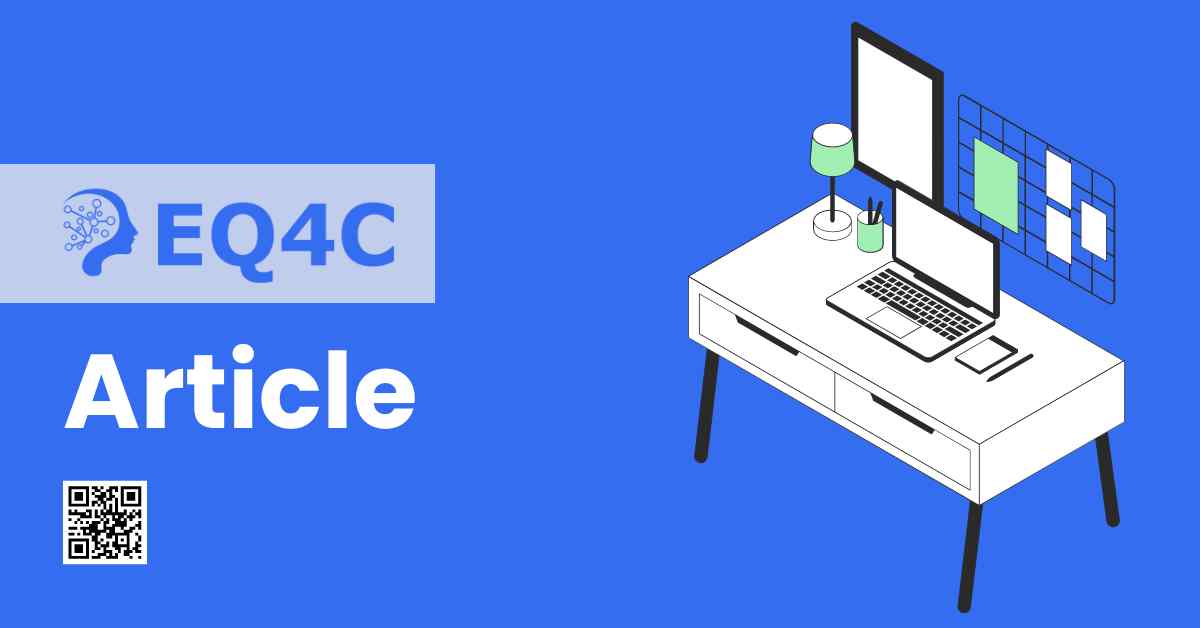
What is Lean Management?
Definition of Lean Management
Lean management is a business philosophy and set of techniques that strive to eliminate waste and improve efficiency in all aspects of an organization.
The goal of lean management is to maximize value for the customer while minimizing waste and inefficiencies.
This is achieved by identifying and eliminating non-value adding activities, streamlining processes, and empowering employees to take ownership of their work and continuously improve it.
Brief history of Lean Management
The origins of lean management can be traced back to the manufacturing industry in the early 20th century, specifically to the Toyota Production System developed by Taiichi Ohno. Ohno identified seven types of waste: overproduction, waiting, defects, overprocessing, unnecessary motion, inventory, and unused talent.
By identifying and eliminating these wastes, Ohno was able to create a highly efficient production system that became the foundation for the lean management philosophy.
In the 1980s, American manufacturers began to adopt lean principles in their own operations, with the goal of improving competitiveness in the global market.
The term “lean” was first coined in the 1990s by John Krafcik, who wrote a seminal article on the topic for the International Motor Vehicle Program at MIT. Since then, lean management has been widely adopted across a variety of industries, from manufacturing and healthcare to software development and service-based industries.
Importance of Lean Management in today’s business environment
Lean management has become increasingly important in today’s business environment as organizations face intense pressure to reduce costs, improve efficiency, and increase responsiveness to customer needs.
The principles of lean management, such as eliminating waste and empowering employees, can help organizations achieve these goals while also improving overall quality and customer satisfaction.
Additionally, lean management techniques can help organizations to become more agile and adaptable in the face of rapidly changing markets and technology.
The ability to continuously improve processes and products is critical for organizations looking to stay competitive and grow in today’s fast-paced business environment.
Principles of Lean Management
Identifying and Eliminating Waste
The first principle of lean management is identifying and eliminating waste. Waste, in the context of lean management, refers to any activity or process that does not add value to the product or service being delivered to the customer.
Common types of waste include overproduction, waiting, defects, overprocessing, unnecessary motion, inventory, and unused talent.
By identifying and eliminating these wastes, organizations can improve efficiency, reduce costs, and increase quality.
One common tool used to identify waste is value stream mapping, which involves analyzing the entire process from raw materials to finished product, and identifying any non-value-adding steps that can be eliminated.
Continuous Improvement
Continuous improvement is another key principle of lean management. The goal of continuous improvement is to continuously identify and implement small changes that lead to big improvements over time.
This is achieved by creating a culture of continuous improvement, where employees are empowered to identify problems and suggest solutions.
Employees are also trained to look for ways to improve processes and products, with the goal of creating a culture of constant learning and development. Continuous improvement is often achieved through the use of tools such as Kaizen, which is a Japanese term meaning “improvement” or “change for the better.”
Respect for People
Lean management also emphasizes respect for people. This principle acknowledges that employees are the backbone of any organization and should be treated with respect and dignity.
By creating a culture where employees feel valued and respected, organizations can improve employee engagement, motivation, and retention. This, in turn, leads to a more productive and efficient workforce.
Focus on Value
Another principle of lean management is a focus on value. This principle is all about understanding what the customer wants and delivering it in the most efficient and effective way possible.
By focusing on value, organizations can better understand their customers’ needs and create products and services that meet those needs, which leads to increased customer satisfaction and loyalty.
Flow and Pull Systems
The final principle of lean management is flow and pull systems. The idea behind flow is to create a smooth and efficient process, where work flows seamlessly from one step to the next.
The goal is to minimize delays and bottlenecks, so that work is completed quickly and efficiently. Pull systems, on the other hand, are based on the principle of “pulling” work through the process only as it is needed, rather than “pushing” work through the process regardless of customer demand.
This helps to reduce overproduction and inventory waste, while also improving responsiveness to customer demand.
Implementation of Lean Management
Identifying Value Streams
The first step in implementing lean management is identifying the value streams within an organization. A value stream is the series of activities that a product or service goes through, from raw materials to the customer.
By identifying the value streams, organizations can better understand the flow of work and where inefficiencies and waste may exist. This can be done through value stream mapping, which is a tool that helps to visualize the entire process and identify areas for improvement.
Mapping the Current Process
Once value streams have been identified, the next step is to map the current process. This involves breaking down the process into smaller steps and analyzing each step in detail.
The goal is to understand how the process currently works, so that improvements can be made. This can be done through process mapping, which is a tool that helps to visualize the process and identify bottlenecks, delays, and other inefficiencies.
Identifying and Eliminating Waste
Once the process has been mapped, the next step is to identify and eliminate waste. Waste, as defined in lean management, refers to any activity or process that does not add value to the product or service.
By identifying and eliminating waste, organizations can improve efficiency, reduce costs, and increase quality. This can be done through tools such as value stream mapping and process mapping, which can help to identify areas of waste.
Implementing Flow and Pull Systems
Once waste has been eliminated, the next step is to implement flow and pull systems. Flow systems aim to create a smooth and efficient process, where work flows seamlessly from one step to the next.
Pull systems, on the other hand, are based on the principle of “pulling” work through the process only as it is needed, rather than “pushing” work through the process regardless of customer demand. These systems help to reduce overproduction and inventory waste, while also improving responsiveness to customer demand.
Establishing a Continuous Improvement Culture
Another important aspect of implementing lean management is establishing a culture of continuous improvement. This involves creating a culture where employees are empowered to identify problems and suggest solutions.
Employees are also trained to look for ways to improve processes and products, with the goal of creating a culture of constant learning and development.
Empowering Employees
Lastly, empowering employees is crucial for the successful implementation of lean management. By giving employees the tools, training, and autonomy to make decisions, organizations can improve employee engagement, motivation, and retention.
This, in turn, leads to a more productive and efficient workforce. Empowering employees also facilitates the continuous improvement culture, as employees are more likely to identify problems and suggest solutions when they feel valued and respected.
Lean Management Tools and Techniques
Value Stream Mapping
Value stream mapping is a tool that helps organizations to understand the flow of work, from raw materials to finished product, and identify areas for improvement.
This is done by creating a visual representation of the entire process, which allows organizations to see where inefficiencies and waste exist. Value stream mapping can be used to identify non-value-adding steps that can be eliminated, as well as to identify bottlenecks, delays, and other inefficiencies in the process.
Kanban
Kanban is a tool that helps organizations to visualize the flow of work and manage inventory. It is based on the pull system principle, which means that work is “pulled” through the process only as it is needed, rather than “pushed” through the process regardless of customer demand.
Kanban boards are commonly used, which are visual boards that display the status of work items, such as work in progress, completed work, and work that needs to be done. The goal of Kanban is to reduce overproduction and inventory waste, while also improving responsiveness to customer demand.
5S
5S is a tool that helps organizations to improve the organization and cleanliness of the workplace. 5S stands for Sort, Set in Order, Shine, Standardize, and Sustain. The goal of 5S is to create a clean, organized, and safe work environment, which can lead to improved efficiency and productivity.
Standardized Work
Standardized work is a tool that helps organizations to define and document the most efficient way to perform a specific task.
By standardizing work, organizations can ensure that all employees are performing tasks in the same way, which can lead to improved efficiency and quality.
Standardized work also serves as a foundation for continuous improvement, as it allows employees to identify problems and suggest solutions.
Total Productive Maintenance (TPM)
Total Productive Maintenance (TPM) is a tool that helps organizations to improve the overall performance of equipment and machinery.
TPM is a maintenance strategy that involves the active participation of employees in the maintenance of equipment, with the goal of achieving maximum equipment efficiency.
By involving employees in the maintenance process, organizations can reduce downtime and improve equipment reliability.
Root Cause Analysis
Root Cause Analysis (RCA) is a tool that helps organizations to identify the underlying cause of a problem. RCA is a problem-solving tool that is used to identify the root cause of an issue, so that it can be permanently resolved.
By identifying the root cause of a problem, organizations can prevent recurrence of the problem and improve overall process efficiency. Common RCA methodologies include 5 Whys and Fishbone diagrams.
Lean Management in Action
Case Studies of Successful Lean Implementations
Lean management has been successfully implemented in a wide range of industries and organizations. One well-known example is the implementation of lean principles at Toyota, which led to the development of the highly efficient Toyota Production System.
Other successful examples include the implementation of lean principles in healthcare organizations, such as Virginia Mason Medical Center, which has been able to reduce costs and improve patient outcomes through the use of lean techniques. In manufacturing, Boeing was able to improve efficiency and reduce costs by implementing lean principles in their production process.
Best Practices for Lean Management
There are several best practices that organizations can follow to successfully implement lean management:
- Start small: it’s best to start with a small, well-defined project that allows the organization to gain experience with lean tools and techniques.
- Involve everyone: Lean management is most effective when everyone in the organization is involved in the process of continuous improvement.
- Identify and eliminate waste: Start by identifying and eliminating waste in the process, this is the most effective way to improve efficiency and reduce costs.
- Establish a culture of continuous improvement: Create a culture where employees feel empowered to identify problems and suggest solutions.
- Focus on flow: Focus on creating a smooth and efficient process, where work flows seamlessly from one step to the next.
Common Challenges and How to Overcome Them
There are several challenges that organizations may face when implementing lean management:
- Resistance to change: Employees may be resistant to change, especially if they are used to working in a certain way. To overcome this, it’s important to involve employees in the process of change and to clearly communicate the benefits of lean management.
- Lack of leadership: Lean management requires strong leadership to be successful. Without strong leadership, it may be difficult to create a culture of continuous improvement.
- Difficulty in identifying waste: It may be difficult to identify areas of waste in the process. To overcome this, organizations can use tools such as value stream mapping and process mapping to visualize the process and identify areas of waste.
- Difficulty in measuring progress: It may be difficult to measure progress when implementing lean management. To overcome this, organizations can use metrics such as cycle time, lead time, and inventory turnover to measure progress.
Conclusion
Recap of key points
Lean management is a business philosophy and set of techniques that strive to eliminate waste and improve efficiency in all aspects of an organization.
The key principles of lean management include identifying and eliminating waste, continuous improvement, respect for people, focus on value, and flow and pull systems.
To implement lean management, organizations can identify value streams, map the current process, identify and eliminate waste, implement flow and pull systems, establish a culture of continuous improvement, and empower employees.
Future of Lean Management
As organizations continue to face intense pressure to reduce costs, improve efficiency, and increase responsiveness to customer needs, the future of lean management looks bright. Organizations are increasingly looking for ways to become more agile and adaptable in the face of rapidly changing markets and technology. The ability to continuously improve processes and products is critical for organizations looking to stay competitive and grow. The future of lean management will likely see an increased emphasis on digital technologies such as automation and data analytics, which will help organizations to identify waste and improve efficiency in new ways.
How to get started with Lean Management in your organization
To get started with lean management in an organization, there are several steps that can be taken:
- Conduct a thorough assessment of the current process to identify areas for improvement.
- Involve employees in the process of change, and communicate the benefits of lean management.
- Start small with a well-defined project to gain experience with lean tools and techniques.
- Establish a culture of continuous improvement, and involve employees in the process of continuous improvement.
- Measure progress and use metrics such as cycle time, lead time, and inventory turnover to track progress.
It’s important to note that lean management is not a one-time event, it’s a journey of continuous improvement, so it’s important to be patient, persistent and to have a long-term commitment.
Read More About: Leadership Skills, Management Theories