Total Quality Management (TQM)
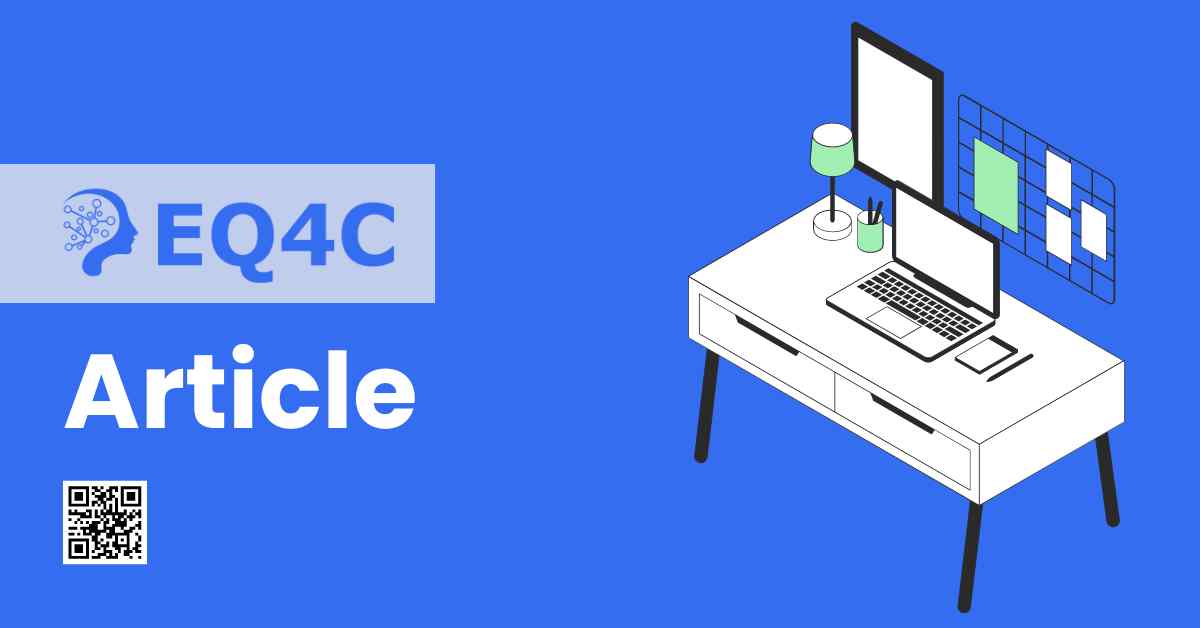
What is Total Quality Management (TQM)?
Total Quality Management (TQM) is a management approach that focuses on continuous improvement and customer satisfaction. It is a holistic approach that involves all employees in the organization in a process of continuous improvement, with the goal of achieving high levels of quality in all aspects of the organization’s operations.
The main principles of TQM include:
- A strong customer focus, with the goal of meeting or exceeding customer expectations.
- The involvement of all employees in the organization in the quality improvement process.
- The use of data and analysis to drive decision-making and to measure progress.
- A focus on continuous improvement, with the goal of constantly improving the organization’s processes and products.
- The use of teamwork, communication, and collaboration to achieve common goals.
TQM is based on the belief that quality is the responsibility of every member of the organization, and that everyone has a role to play in improving it. It is also based on the idea that quality improvement is a never-ending process and that it requires constant attention and effort.
TQM has been widely used in many industries such as manufacturing, healthcare, and service industries. It has been used to improve the quality of products and services, to reduce costs, and to improve customer satisfaction. TQM can be applied in both private and public organizations, and it can be adapted to suit the needs of different types of organizations.
What are Primary elements of Total Quality Management (TQM)?
The 8 primary elements of Total Quality Management (TQM) are:
- Leadership: TQM requires strong leadership at all levels of the organization, with leaders who are committed to quality and who provide the direction and support needed to achieve quality goals.
- Strategic Planning: TQM requires a clear strategic plan that sets out the organization’s quality goals and objectives and defines how they will be achieved.
- Customer Focus: Total Quality Management (TQM)M requires a strong focus on meeting or exceeding customer needs and expectations, and on building customer loyalty.
- Employee Involvement: TQM requires the active involvement of all employees in the quality improvement process, with the goal of empowering them to take ownership of quality and to continuously improve their work.
- Continuous Improvement: TQM requires a focus on continuous improvement, with the goal of constantly improving the organization’s processes and products.
- Performance Measurement: Total Quality Management (TQM) requires the use of data and analysis to measure performance, to identify areas for improvement, and to track progress.
- Communication: TQM requires effective communication at all levels of the organization, with the goal of ensuring that everyone is informed, engaged, and aligned with the organization’s quality goals.
- Teamwork: TQM requires the use of teamwork, collaboration, and cooperation to achieve common goals, and to build a culture of trust and respect.
These 8 elements of Total Quality Management (TQM) are interrelated, and they all play a critical role in achieving high levels of quality. By implementing TQM, organizations can improve the quality of their products and services, reduce costs, and increase customer satisfaction.
What are the Benefits of TQM?
Total Quality Management (TQM) can bring a variety of benefits to an organization, some of them include:
- Improved Quality: TQM focuses on continuous improvement, which can lead to better quality products and services, fewer defects and errors, and higher customer satisfaction.
- Increased Efficiency: TQM focuses on eliminating waste and inefficiencies in processes, which can lead to increased productivity and efficiency.
- Reduced Costs: By improving quality and efficiency, Total Quality Management (TQM) can help reduce costs associated with rework, defects, and customer complaints.
- Improved Customer Satisfaction: TQM focuses on meeting or exceeding customer needs and expectations, which can lead to increased customer loyalty and satisfaction.
- Increased Employee Involvement and Motivation: TQM involves all employees in the quality improvement process, which can lead to increased employee involvement, empowerment and motivation.
- Improved communication and teamwork: Total Quality Management (TQM) promotes effective communication and teamwork throughout the organization, which can lead to better decision making and problem solving.
- Enhanced Reputation: TQM can help an organization build a reputation for quality, which can lead to increased business and new opportunities.
- Better decision making: TQM encourages the use of data and analysis to make decisions and track progress.
What is the History and evolution of TQM?
The concept of Total Quality Management (TQM) has evolved over time, and it has its roots in several different management approaches and movements:
- The Quality Control Movement: The Quality Control Movement, which began in the 1920s, was the first major effort to focus on quality in the manufacturing industry. It emphasized the importance of inspection and testing to ensure the quality of products.
- Statistical Quality Control: Statistical Quality Control, which began in the 1930s, was a more systematic approach to quality control that used statistical tools and techniques to identify and control sources of variability and defects.
- The Quality Control Circle Movement: The Quality Control Circle Movement, which began in Japan in the 1950s, was an effort to involve all employees in the quality control process and to create a culture of quality.
- The Total Quality Control Movement: The Total Quality Control Movement, which began in Japan in the 1960s, was an effort to extend the focus of quality control beyond the factory floor to the entire organization. It emphasized the importance of leadership, customer focus, and continuous improvement.
- Total Quality Management (TQM): TQM, which began in the 1980s, was an effort to further refine and expand the Total Quality Control Movement. It emphasized the importance of involving all employees in the quality improvement process, and it focused on the use of data and analysis to drive decision-making and measure progress.
TQM was widely used in Japan and other Asian countries in the 1980s, and it started to gain popularity in the United States and other Western countries in the 1990s.
How to Implement Total Quality Management (TQM)?
Implementing Total Quality Management (TQM) can be a complex and challenging process, but it can be broken down into several key steps:
- Establish a clear vision and mission: Define the organization’s overall quality goals and objectives and communicate them to all employees.
- Assess the current situation: Conduct a thorough assessment of the organization’s current quality systems, processes, and practices, and identify areas for improvement.
- Involve employees: Involve all employees in the implementation process, and ensure that they understand their role in achieving quality goals.
- Develop a quality plan: Develop a detailed quality plan that sets out specific goals and objectives, and defines how they will be achieved.
- Implement quality systems: Implement quality systems and processes, such as quality control and quality assurance, to ensure that products and services meet or exceed customer expectations.
- Measure and track performance: Use data and analysis to measure performance, to identify areas for improvement, and to track progress.
- Continuously improve: Continuously improve the organization’s quality systems, processes, and practices, with the goal of achieving high levels of quality.
- Recognize and reward success: Recognize and reward employees for their contributions to quality improvement and for achieving quality goals.
It’s important to note that implementing TQM requires a long-term commitment, and it requires a cultural change in the organization.
It’s not a one-time event, but an ongoing process. TQM also requires strong leadership, effective communication, and the active involvement of all employees.
By following these steps and continuously improving, organizations can achieve high levels of quality and improve the overall performance of the organization.
What are Deming’s 14 Points for Total Quality Management (TQM)?
Deming’s 14 Points for Total Quality Management (TQM) are a set of principles for improving the quality and effectiveness of an organization, developed by W. Edwards Deming. The 14 points are:
- Create constancy of purpose for improving products and services: Develop a clear vision and mission for the organization, and ensure that all employees understand their role in achieving quality goals.
- Adopt the new philosophy: Embrace a new philosophy of quality, which emphasizes the importance of continuous improvement, customer focus, and employee involvement.
- Cease dependence on mass inspection: Instead of relying on mass inspection, use statistical techniques and quality control to identify and control sources of variability and defects.
- End the practice of awarding business on the basis of price tag: Award business on the basis of quality, service, and long-term relationships.
- Improve constantly and forever the system of production and service: Continuously improve the organization’s processes and systems, with the goal of achieving high levels of quality.
- Institute training on the job: Provide training for all employees, with the goal of developing their skills and knowledge.
- Institute leadership: Develop strong leadership at all levels of the organization, with leaders who are committed to quality and who provide the direction and support needed to achieve quality goals.
- Drive out fear: Create a positive work environment where employees feel safe to speak up and share their ideas.
- Break down barriers between staff areas: Encourage communication and collaboration among all employees, with the goal of breaking down barriers between different departments and functions.
- Eliminate slogans, exhortations, and demands for new programs: Instead of relying on slogans and exhortations, focus on achieving measurable results through continuous improvement.
- Eliminate numerical quotas: Eliminate numerical quotas, which can lead to an emphasis on meeting targets at the expense of quality.
- Remove barriers to pride of workmanship: Remove barriers to pride of workmanship, such as poor working conditions and lack of recognition, so that employees can take pride in their work.
- Institute a vigorous program of education and retraining: Provide ongoing education and retraining for all employees, with the goal of developing their skills and knowledge.
- Take action to accomplish the transformation: Take action to implement the changes needed to achieve high levels of quality and performance, and to continuously improve the organization.
These 14 points are a guide for implementing TQM, they emphasize the importance of continuous improvement, customer focus, and employee involvement.
They also stress the need for strong leadership, effective communication, and ongoing education and training.
By following these principles, organizations can improve the quality of their products and services, reduce costs, and increase customer satisfaction.
Conclusion
The approach has been adapted and evolved over time to suit different types of organizations, cultures and industries. Today, TQM is considered as a holistic approach to management that is widely used to improve the quality, efficiency, and effectiveness of organizations.
- British Library. “W Edwards Deming.”
Read More About: Leadership Skills, Management Theories